The Science Behind Porosity: A Comprehensive Guide for Welders and Fabricators
Recognizing the elaborate mechanisms behind porosity in welding is critical for welders and fabricators pursuing impressive craftsmanship. As metalworkers explore the midsts of this phenomenon, they discover a world governed by numerous variables that affect the formation of these tiny voids within welds. From the structure of the base materials to the details of the welding process itself, a wide range of variables conspire to either worsen or reduce the visibility of porosity. In this comprehensive guide, we will unwind the scientific research behind porosity, discovering its results on weld high quality and unveiling progressed methods for its control. Join us on this trip through the microcosm of welding blemishes, where accuracy fulfills understanding in the pursuit of perfect welds.
Comprehending Porosity in Welding
FIRST SENTENCE:
Evaluation of porosity in welding exposes critical insights into the honesty and top quality of the weld joint. Porosity, characterized by the visibility of tooth cavities or gaps within the weld steel, is an usual problem in welding processes. These voids, otherwise properly resolved, can endanger the structural integrity and mechanical buildings of the weld, causing possible failings in the completed item.
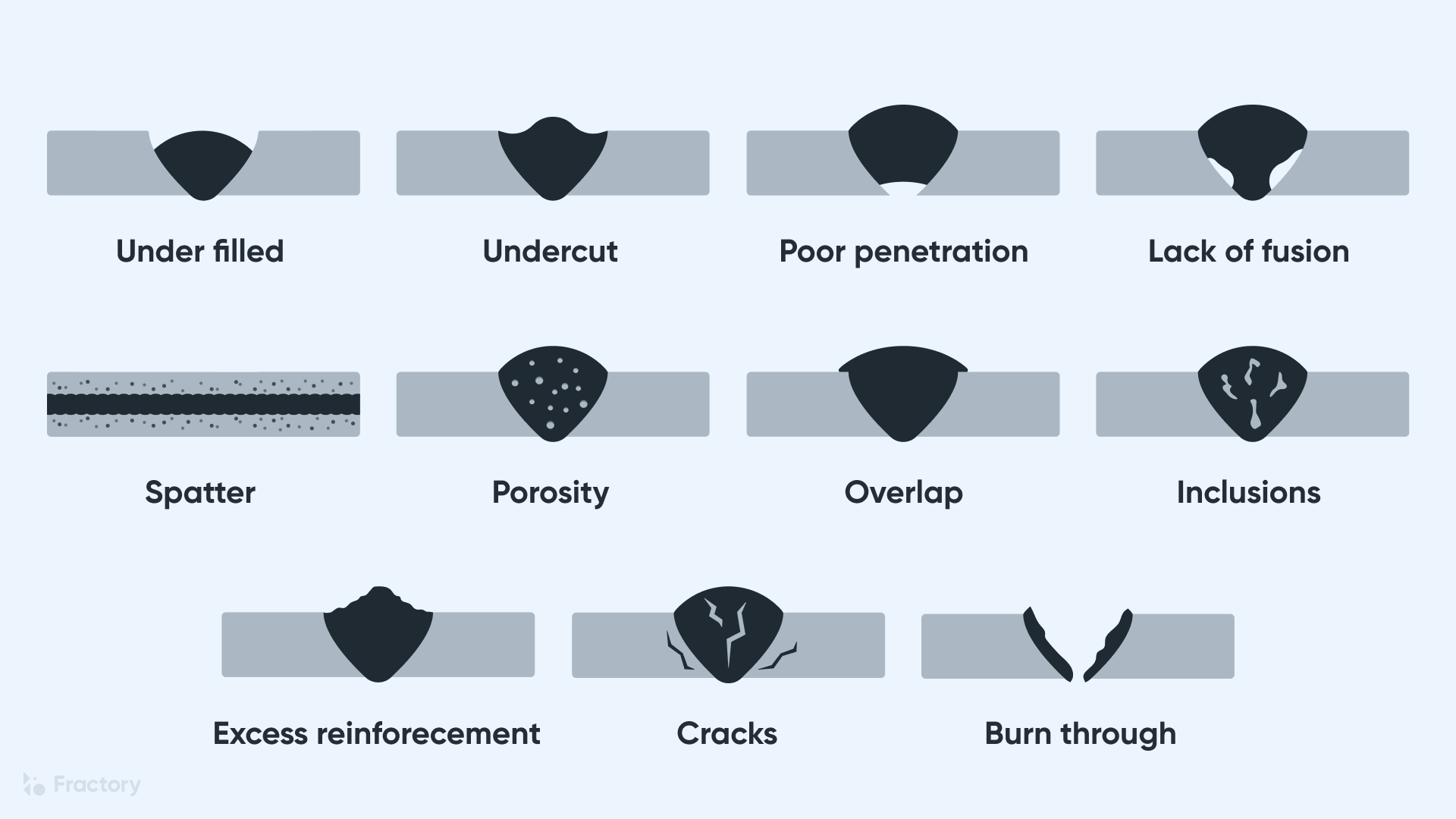
To spot and quantify porosity, non-destructive screening approaches such as ultrasonic testing or X-ray evaluation are typically used. These methods permit the recognition of interior defects without endangering the integrity of the weld. By examining the size, form, and distribution of porosity within a weld, welders can make informed decisions to improve their welding processes and achieve sounder weld joints.
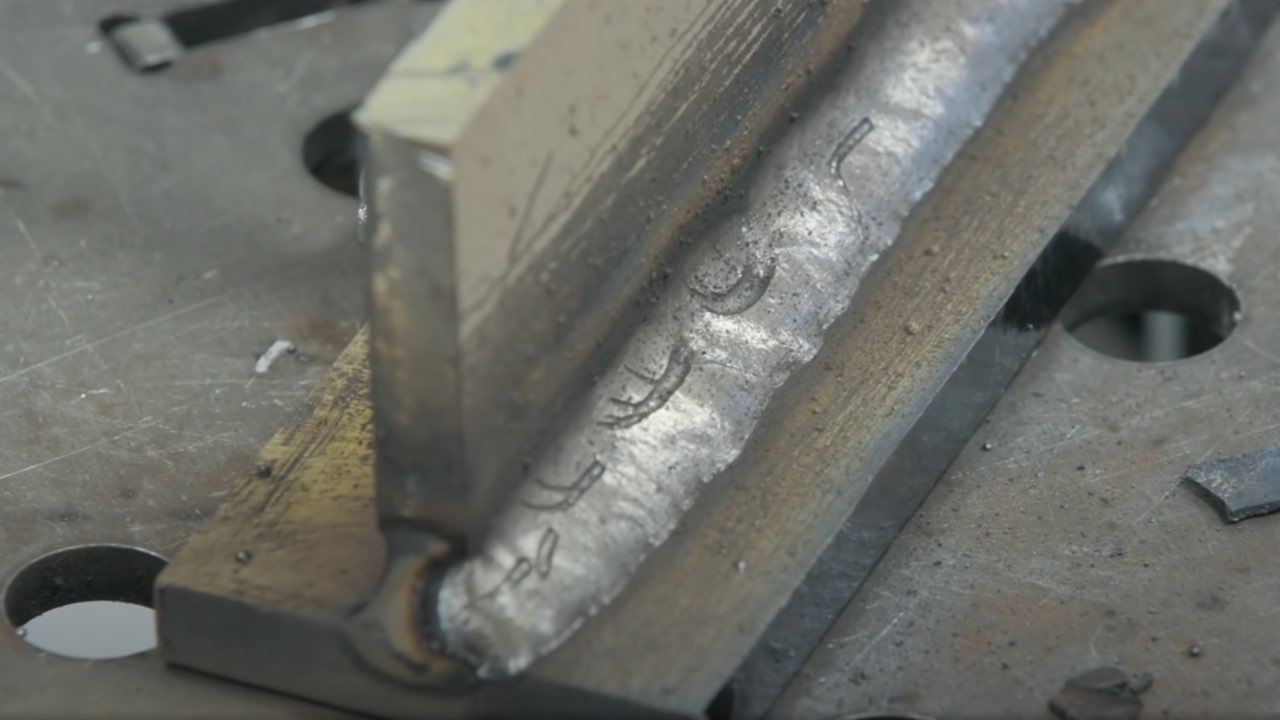
Elements Influencing Porosity Formation
The occurrence of porosity in welding is affected by a myriad of elements, varying from gas shielding performance to the complexities of welding specification setups. Welding parameters, including voltage, present, travel rate, and electrode type, also effect porosity development. The welding technique used, such as gas metal arc welding (GMAW) or protected metal arc welding (SMAW), can affect porosity see this website development due to variants in warmth distribution and gas coverage - What is Porosity.
Effects of Porosity on Weld High Quality
Porosity development considerably jeopardizes the architectural stability and mechanical residential or commercial properties of bonded joints. When porosity is existing in a weld, it develops voids or tooth cavities within the product, reducing the overall stamina of the joint. These gaps serve as anxiety focus factors, making the weld more susceptible to splitting and failure under load. The existence of porosity also weakens the weld's resistance to rust, as the trapped air or gases within the voids can respond with the surrounding setting, leading to degradation over time. In addition, porosity can hinder the weld's capacity to hold up against pressure or impact, Your Domain Name additional jeopardizing the general top quality and dependability of the welded structure. In vital applications such as aerospace, vehicle, or structural constructions, where safety and durability are extremely important, the detrimental results of porosity on weld quality can have severe effects, stressing More Bonuses the relevance of lessening porosity with proper welding techniques and treatments.
Techniques to Minimize Porosity
In addition, making use of the appropriate welding parameters, such as the right voltage, existing, and take a trip rate, is important in stopping porosity. Keeping a consistent arc size and angle during welding additionally aids reduce the likelihood of porosity.

Using the ideal welding method, such as back-stepping or employing a weaving movement, can additionally assist distribute warmth evenly and minimize the chances of porosity formation. By implementing these techniques, welders can efficiently decrease porosity and produce high-quality welded joints.
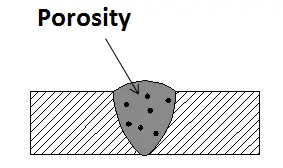
Advanced Solutions for Porosity Control
Implementing advanced innovations and innovative approaches plays a crucial role in accomplishing superior control over porosity in welding processes. In addition, utilizing innovative welding strategies such as pulsed MIG welding or modified atmosphere welding can likewise help reduce porosity problems.
An additional sophisticated remedy involves using innovative welding tools. Using tools with built-in functions like waveform control and innovative power resources can boost weld quality and reduce porosity threats. In addition, the execution of automated welding systems with specific control over criteria can dramatically reduce porosity problems.
In addition, integrating innovative tracking and assessment innovations such as real-time X-ray imaging or automated ultrasonic testing can help in discovering porosity early in the welding process, permitting instant rehabilitative actions. On the whole, integrating these sophisticated services can significantly enhance porosity control and enhance the overall top quality of welded parts.
Verdict
In verdict, comprehending the scientific research behind porosity in welding is vital for welders and producers to produce top quality welds - What is Porosity. Advanced options for porosity control can further improve the welding process and make certain a strong and trustworthy weld.